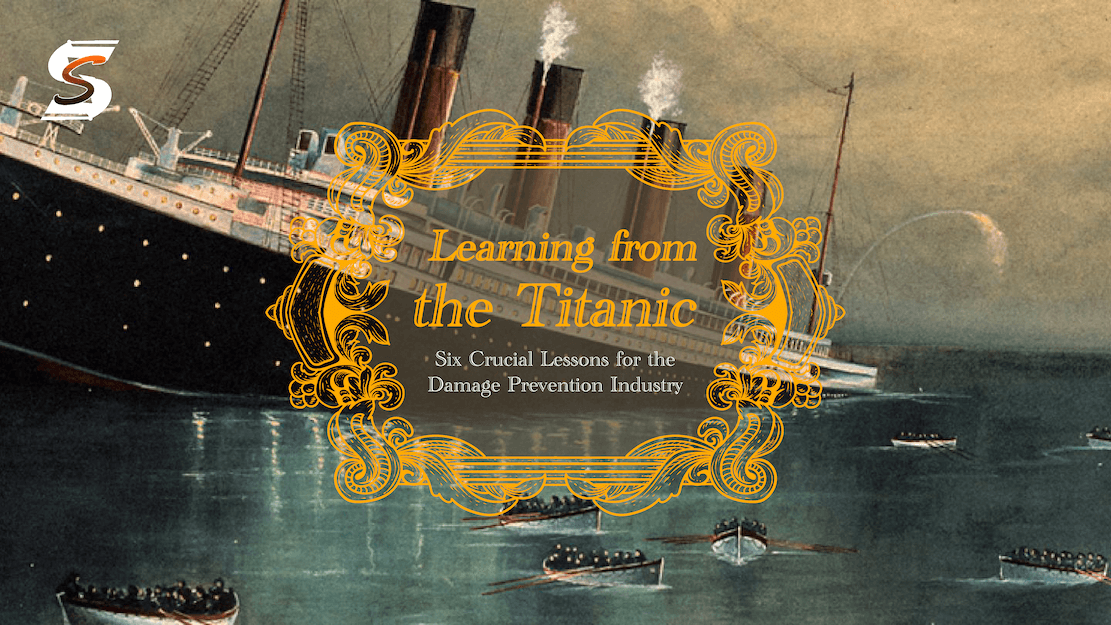
I was at a friend’s house the other day, and they were reading a book about survivors' stories from the Titanic tragedy. I couldn't help but think about the lessons we can learn from the mistakes made back then. With a bit of googling, I found an insightful article by James B. Battles, PhD, originally written for the medical field. It struck me that these lessons are incredibly relevant to the damage prevention and utility locating industry. The tragic sinking of the Titanic in 1912, despite being touted as an unsinkable marvel, offers valuable lessons on how human error, inadequate resources, and miscommunication can lead to disaster. Here are six essential lessons drawn from the Titanic tragedy that can enhance safety and efficiency in our work.
1. Identify System Weak Points Before an Adverse Event Happens
The Titanic's designers knew about potential weak points, such as the limited number of lifeboats and the design of the bulkheads. However, these issues were not adequately addressed before the ship set sail. Similarly, in our industry, proactively identifying and addressing weak points in systems and processes can prevent significant incidents. Regular audits and risk assessments are crucial. Ensuring that potential hazards are identified and mitigated before commencing any excavation or utility work is essential. As Battles notes, "The British have defined risk as the possibility or probability of occurrence or recurrence of an event multiplied by the severity of the event." Detection is the first step in error prevention; undetected errors can have disastrous consequences.
2. Report Near Misses and No-Harm Events
The iceberg warnings received by the Titanic were not taken seriously, underscoring the importance of recognizing and acting upon near misses. Near misses and no-harm events offer critical insights into potential risks that, if addressed, can prevent future accidents. We should encourage the reporting of all near misses and minor incidents. Battles highlights that "a high reporting rate indicates a high detection sensitivity level (DSL), and a low reporting rate indicates a low DSL. To achieve a high DSL, an organization must eliminate impediments to reporting; confidential, no-fault reporting is usually the most successful approach."
3. Encourage Reporting
Post-disaster investigations of the Titanic revealed critical details about the lack of adequate safety measures and missteps. Transparent communication is vital. A ticket management system like Utilocate is beneficial in this regard, as it allows tracking of locator productivity and presents their work, good or bad, in raw figures. Data quickly unravels excuses and enables managers to make informed and supported decisions. Learning from past mistakes is essential, and safety culture thrives when this information is made transparent. We must foster an open culture where employees are encouraged to report hazards and unsafe practices. Confidential, no-fault reporting systems are often the most effective in promoting high detection sensitivity levels (DSL) and with the right TMS you don’t need to worry about where the blame lies - the data will show you."As the amount of information goes up, risk will eventually go down," Battles asserts.
4. Look for Root Causes
The root causes of the Titanic disaster went beyond the immediate iceberg collision, encompassing deeper issues like insufficient lifeboats and flawed safety regulations. Understanding root causes is essential for developing effective strategies to prevent recurrence. Conducting thorough root cause analyses for every incident, investigating who, what, where, when, and why to uncover underlying systemic issues, is vital. This approach prevents stopping at human failure and missing systemic flaws. "The investigators must get to the root causes and discover the latent errors. Otherwise, if they start with a human failure, they can stop there and fail to fix the system," Battles advises. Having a ticket management system where all your data is compiled and can be accessed, leveraged and output is critical for comprehensive investigations
5. Avoid the Blame-and-Train Trap
Blaming individuals, such as Captain Smith or Wireless Officer Phillips, for the Titanic disaster does not address the systemic issues that led to it. In our industry, blaming and retraining employees after an incident is insufficient. It does not address deeper systemic issues. We should focus on improving systems and processes rather than assigning blame. Use incidents as learning opportunities to make systemic changes that enhance safety. Battles emphasizes, "We must stop blaming people and start looking at our systems. We must look at how we do things that cause errors and keep us from discovering them before they cause an injury."
6. Fix the Latent Errors that Set People Up for Failure
Latent errors, such as the inadequate number of lifeboats and the flawed design of the watertight compartments, contributed significantly to the Titanic disaster. In our field, latent errors in systems and processes can predispose individuals to make mistakes, leading to potentially disastrous outcomes. Identifying and correcting latent errors in our systems is crucial. Design processes that support safe and efficient work practices, reducing the likelihood of human error. Battles notes that "many disasters have a major management organizational component. Technical errors, instead, tend to lead to much less severe problems."
Conclusion
The lessons from the Titanic disaster underscore the importance of proactive safety measures, effective communication, and a reporting culture in preventing incidents. By applying these principles, the damage prevention and utility locating industries can create safer work environments, minimize risks, and ensure preparedness for unforeseen challenges. As we learn from past mistakes, we can build a future where safety and efficiency go hand in hand.
Share this Post